Sun-Soaked West Virginia Home Goes Net Zero
Last Updated: Apr 11, 2025When Rita Hennessy and Sean Palmer starting planning for retirement, one of their priorities was moving into an energy-efficient home. For decades, the couple had lived in a drafty, post-war cinder block and brick home near Charles Town, West Virginia. Their energy source: West Virginia’s coal-powered electrical grid.
She was a park ranger with the Appalachian National Scenic Trail; he was an engineer for a biotech company. They’re both concerned about climate change. They wanted to reduce their carbon footprint. They also wanted to live in a home more aligned with their values.
Table of Contents
- High-Performance Systems
- Heat and Pizza
- Open Space, Reclaimed Timbers
They found a property with good southern exposure, as their hearts were set on a passive solar design and a PV system. Then they found architect Debra Rucker Coleman of Sun Plans Inc., in Alabama.
The couple selected a home design from Sun Plans’ website. Coleman had them complete her Adapt-A-SunPlan process, as they proposed several alterations. “The changes they required to the pre-designed plan were so drastic,” Coleman says, “that I would have spent more time, and it would have been more expensive, to make the changes than creating a new design.” So Coleman designed a new house plan for them, which is now known as the RISE house (named for the couple, the RI stands for Rita, the SE for Sean).
The couple initially thought they could make do with 1,500 square feet. They soon realized they needed more kitchen space and a larger common area for entertaining. (They like to host fundraisers and dinner parties for their local Audubon chapter.) They also decided to add a 287-square-foot loft, which has a row of south-facing clerestory windows (operated by remote control) that draw out warm air in the summer and bring in lots of daylight.
In 2012, they completed the 2,148-square-foot RISE home outside of Shepherdstown. The spacious three-bedroom, two-bath home is anchored by a large masonry wood stove that provides supplemental heat during the winter—and includes a pizza oven. The home’s battery-less, grid-tied solar electric system, powered by a solar array on the south-facing roof, has taken the home to zero-net energy. It also fuels the couple’s electric car.
High-Performance Systems
Coleman oriented the home 10-degrees east of south to reduce heat gain during the summer, and maximize solar gain during the winter. She also designed window overhangs that do the same. Double-pane, fiberglass-framed casement and awning windows incorporate a maximum U-factor of 0.28. (The lower the U-factor, the higher the insulation properties and the windows’ resistance to heat transfer.)
The house is oriented to capture the winter sun through those windows and passively heat the home. The four-inch-thick, concrete slab-on-grade floor has three inches of rigid-foam insulation with an R-value of 15. The doubled two-by-four stick-frame walls are on 16-inch centers with a half-inch space in-between. The result is an eight-inch-thick wall where fiberglass batts and closed-cell spray foam insulation bring the walls to R-36. The home’s roof was framed with manufactured wood trusses to allow for lots of fiberglass batt and spray foam insulation in the vaulted ceiling.
To combat the region’s hot, humid summer climate, the clerestory was key. “When we open those windows, the hot air goes up and out, while the operable windows on the first level bring cool air in,” Palmer explains. “I can feel the cool air moving across my ankles.” A whole-house fan in the attic also helps move air through the home. In mid-summer, when the high temperatures and humidity last well into the night, the couple turns on their multi-zone mini-split for additional cooling.
Most mini-splits operate like a standard air-source heat pump, with an outdoor condenser/compressor, but without the expense or space required for ducts. In this home, without ducts, conditioned air wouldn’t be able to reach the bedrooms. An eight-inch-tall ducted air handler was concealed in the hallway’s dropped ceiling, to preserve the ceiling’s thermal integrity. The duct runs down the hall to feed into the bedrooms. The ducts were routed in the attic above the primary ceilings and buried under 16 inches of blown-in fiberglass insulation.
The home’s 6.3 kW PV system generates about 700 kWh per month; the house, however, consumes about 563 kWh per month. While the kitchen has a propane cooktop and the wood-burning masonry heater, the home has all-electric appliances. Much of the home’s winter heat comes from the unique, masonry wood stove at the center of the home.
Shop All Special Offers
Shop Special Offers on vetted Home Improvement products at low prices while supplies last.
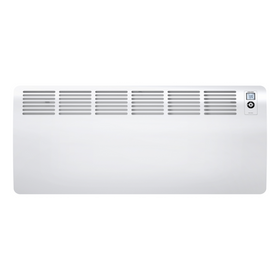
Stiebel Eltron CON 300-2 Premium Wall-Mounted Convection Heater - 202030
Stiebel Eltron
In Stock

Stiebel Eltron Accelera 300 E Heat Pump Water Heater
Stiebel Eltron
In Stock
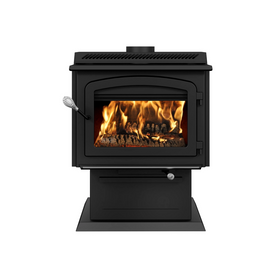
Drolet HT-3000 Wood Burning Stove DB07300
Drolet
In Stock

Victory Range Hood Sunset 600 CFM White Flush Ceiling Mount Dimmable LED Range Hood
Victory Range Hoods
In Stock

Stiebel Eltron DHC-E 8/10-2 Plus Point-of-Use Electric Tankless Water Heater - 202145
Stiebel Eltron
In Stock

Stiebel Eltron CON 150-1 Premium Wall-Mounted Convection Heater - 202026
Stiebel Eltron
In Stock

Stiebel Eltron Accelera 220 E Heat Pump Water Heater
Stiebel Eltron
In Stock

Innovative Dehumidifier IW25-5 In-Wall Dehumidifier
Innovative Dehumidifier
In Stock

Victory Range Hood Sunset 600 CFM Flush Ceiling Mount Dimmable LED Range Hood
Victory Range Hoods
In Stock

Drolet Bistro Wood Burning Cookstove DB04815
Drolet
In Stock
Open Space, Reclaimed Timbers
The windows to the south, which bring in passive solar, overlook the native meadow the couple restored. Inside, they wanted to use reclaimed lumber for the loft and staircase. They found some from an 1880’s woolen factory in Connecticut, close to where Hennessy grew up. The factory worked with recycled or “shoddy” wool. “We like having those in our home and the story to go with it,” she says.
The home’s vaulted ceilings create airy, open living areas. “Rita and Sean wanted a large loft and clerestory for both light and passive cooling, but did not want supporting columns,” Coleman says. “That was a structural challenge. To solve this, we had to use a large beam to hold up the roof of the clerestory.”
The dining room has a large bay window with east, south, and west: the porch blocks most of the late afternoon summer sun. “We might have bumped out the dining room a bit more, to accommodate our dinner parties and entertaining,” Hennessy says. She adds that the couple could use a few more feet in the laundry area, as well. “But these are little things,” Hennessy says.
“We also built this house for aging in place,” Palmer adds. “We’ve cared for elderly parents, so we’re aware of how our home needs to accommodate us in the future. For instance, there’s only one step up into the house. The bedrooms and baths are on one level. When we get to the point where we can’t walk to the mailbox, that’s when we’ll know it’s time to move.”
Camille LeFevre
Camille LeFevre is an architecture and design writer based in the Twin Cities.